Ignition System Comparison Table
Each type of ignition system has a different set of advantages and drawbacks. Engine designers and restorers/tuners have to keep all these tradeoffs in mind when selecting which to use. This table contains an overview of the each system’s characteristics:
System Name | Cost | Weight | Voltage | Efficiency |
---|---|---|---|---|
Magneto (Inductive Discharge) | $ | ⚓ | ⚡ | ★ |
Distributor (Kettering) | $$ | ⚓⚓⚓ | ⚡⚡ | ★★ |
Capacitive Discharge | $$ | ⚓⚓ | ⚡⚡⚡ | ★★ |
Coil‑On‑Plug/Coil‑Near‑Plug | $$$ | ⚓⚓⚓ | ⚡⚡ | ★★★ |
Magneto (Inductive Discharge) Ignition System
Magnetos are the simplest, and lightest ignition system, perfect for two-stroke engines, but inefficient and inconsistent, especially on four-strokes. Magneto ignition systems are most often found on go-karts, lightweight tools, outboard motors, and some small aircraft.
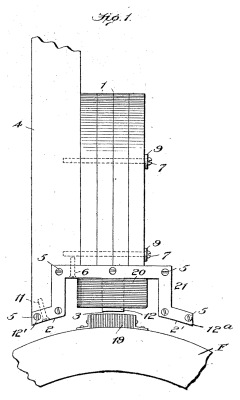
The inductive discharge system consists of a magnet on the flywheel that passes by a fixed electrical coil; the electrical coil is connected to one or two spark plugs, often through a transformer (to boost the voltage) and/or an interrupter (to control the timing). As the magnet passes the coil, it generates a voltage across the coil, which builds up until it (hopefully) produces a spark. This system doesn’t require a battery, and its simplicity makes it very light and reliable, which is perfect for small engines.
One problem with inductive discharge systems is that the voltage they produce, and the size of the spark that they create is dependent on the speed of the magnet (and the engine). Magnetos usually produce much more energetic (higher-powered) sparks at higher RPM. This is good from an ignition point of view, as the fuel-air mixture requires a stronger spark to fully combust when the engine is going faster. The trouble comes from the fact that the magneto must be sized and configured to ensure reliable ignition at low RPM, which means that it is usually over-sized at the high end, so they waste a lot of energy (and fuel); some systems have compensators, which attempt to reduce this wastage, but the compensation adds weight and complexity.
Because the magnet passes the coil once every engine revolution, the system generates a spark at each spark plug on each revolution (unless it has a complicated interrupter); this is perfect for a two-stroke engine, but creates a ‘waste spark‘ on four-cycle engines. On a four-stroke engine with an even number of cylinders, a single magnet and coil can generate sparks for a pair of cylinders, but each additional pair of cylinders requires another coil adjacent to the flywheel, where there isn’t much available real estate. These issues make the magneto system very wasteful and impractical on large engines.
Conventional Distributor Ignition System
The conventional distributor system is also known as the “Kettering ignition”, after its famous inventor, Charles Kettering. Variants of this system were extremely popular on multi-cylinder engines (on cars, trucks, boats, and aircraft) for well over 50 years.
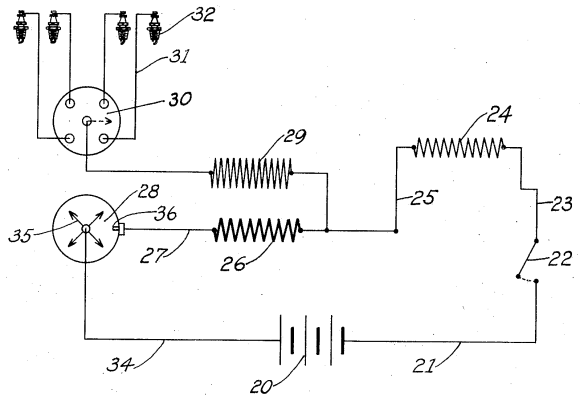
The so-called Kettering ignition system is much more mechanically and electrically complicated than the magneto system, and consists of (at least):
- A battery, which supplies power to the ignition circuit.
- An inductor known as the ‘ignition coil’, which builds up energy in a magnetic field, that can be rapidly discharged into a spark. The ignition coil is usually a transformer, where the ‘primary’ side charges up the field at a low voltage and high current, and the ‘secondary’ side discharges the field at a high voltage and low current.
- A current-limiting resistor, (which may be incorporated in the inductor,) that limits the amount of energy built up in the inductor.
- A distributor, which directs the energy from the inductor into one spark plug, at the appropriate time.
- Spark plugs, which use the electrical energy to create an ‘arc’, that heats the fuel-air mixture, and starts an explosion in a cylinder.
- A (contactor) switch, which allows current to flow through the inductor, but past the sparkplugs, to charge the inductor. This is usually the ‘ignition switch’ on a car.
- Another switch, known as a ‘contact breaker’, which disconnects the contactor from the circuit, and forces the inductor to discharge through the sparkplug.
The Kettering system is much more efficient than the magneto system when used on four-stroke engines, as it doesn’t throw away energy on ‘waste sparks’. This system also produces much more consistent sparks than the magneto, as the current-limiting resistor can ensure that each spark dissipates the same amount of energy; unfortunately, this resistor works by wasting substantial amounts of power, meaning that it the system is not as efficient as other systems, especially at lower engine speeds.
On the other hand, the Kettering system requires a battery and battery-charging system, which add a great deal of weight and cost, making it impractical for very small and light engines. This system also requires a distributor, which must be connected to an engine’s camshaft, which means that the engine requires a heavy and complicated camshaft, and distributor, adding further cost and weight!
Capacitive Discharge Ignition System
The capacitive discharge ignition (CDI) system was probably invented by Nikola Tesla in the 1890s. One notable feature of capacitive discharge ignition systems is their ability to produce extremely large peak voltages, which is one reason they have been so popular in the automotive aftermarket.
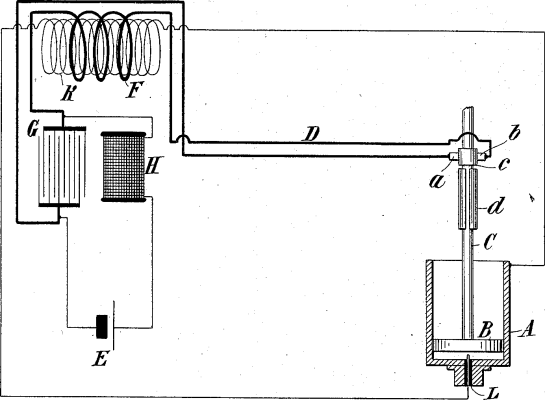
The capacitive discharge system relies on a capacitor, switch, and a transformer to (respectively) store energy then ‘boost’ and release it through a spark plug. The capacitor builds up a charge, usually sourced from a battery or magneto-style generator, and is then discharged through a transformer (similar to the ignition coil used on a Kettering ignition system) by a switch or transistor.
Though the high ‘rated’ output voltage of CDI systems is appealing, it is important to note that a system will never achieve this maximum voltage when used on a real engine, and other specifications (such as total spark energy, dictated by the ignition coil) are usually more important than peak spark voltage. CDI systems are often regarded as relatively fragile and unreliable, due to their reliance on capacitors and transistors, which have (historically) been less dependable than distibutors and mechanical contactors (used on Kettering systems).
Coil-on-Plug and Coil-Near-Plug Systems
Coil-on-plug (COP) and coil-near-plug (CNP) systems are the electronically-controlled counterpart to the Kettering system. Known by various other names (including plug-top or plugtop coils), they were invented in the United Kingdom in the late 1930s, and first introduced in production vehicles in the 1970s.
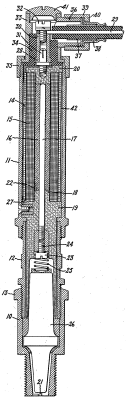
COP and CNP ignitions are very similar to distributor ignition systems, except that they reverse the order of the ‘distributor’ and the voltage transformer. COP systems house the coil right next to the spark plug, usually ‘behind’/’above’ it; CNP systems house the transformer a little further away, and have a short high-voltage spark plug wire between the transformer and spark plug. The ‘electronic distributor’ is (usually) a set of transistors (MOSFETs specifically), controlled and timed by the ECM/ECU.
These systems have a number of benefits when compared to all the others. First, and most importantly, COPs/CNPs are extremely electrically efficient, and produce very consistent and predictable sparks. These systems also allow the ECU/ECM to perform variable ignition timing and advance, to maximize efficiency while preventing knocking/pinging. This computer-control also permits advanced engine diagnostics and efficiency features, such as selective cylinder deactivation.
Unfortunately, this system requires a very complicated power and control system, limiting its use to large and demanding applications, like automotive, large marine, and mass-market motorcycle engines. In terms of reliability, COP and CNP units are exposed to relatively high temperatures and strong vibrations, which can cause failures, especially around the hotter parts of an engine (usually the back/center of the engine bay). These adverse conditions have caused a significant number of failures for a number of manufacturers, due to ignition coil fractures and COP boot cracking.
(Gasoline & Alcohol) Glow Plugs
Gasoline engine glow plugs are very simple heating devices which set off a combustion as soon as the fuel-air mixture comes in contact with the element. They are used in very small model engines, where timing, efficiency, engine life, and pre-detonation (pinging) are low priorities.
What About Diesel Engines?
Which is Best?
The short answer is: it depends!
- Modern cars, pickup trucks, motorcycles, and midsize-large marine engines use coil-on-plug systems, to meet emissions targets/requirements.
- Smaller engines usually depend on magnetos, because they are usually exempted from emissions limits, and put such a high premium on weight.
- Many car restorers and performance-conscious people use capacitive discharge systems, because of the promise of ‘big sparks’.
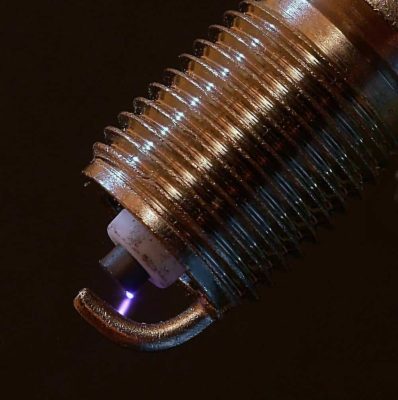
That's All!
If you work on spark-ignition systems, you should take a look at our GTC505 Engine Ignition Analyzer, it was made to help people like you.
If you liked this post, and have a suggestion for a follow-up or unrelated article, please e-mail us the idea, and we’ll get on it!
Thanks for reading our post, we hope you have a great day!